Cleaning Water with a Living Material
Cleaning Water with a Living Material
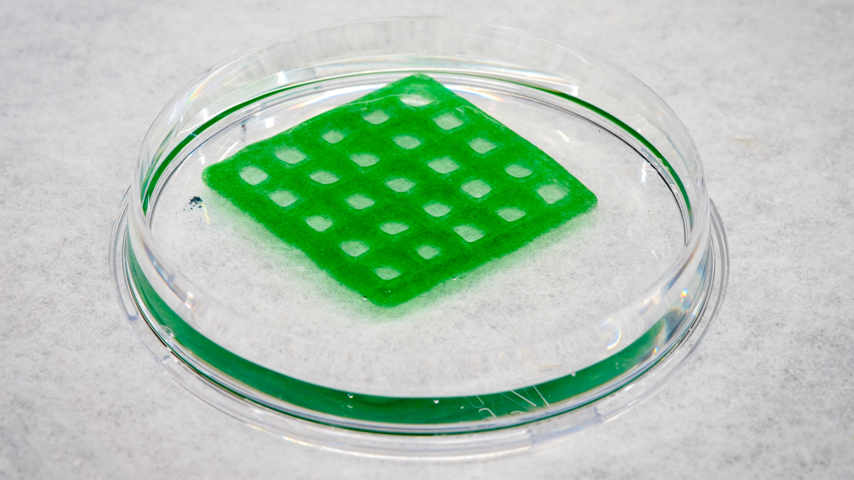
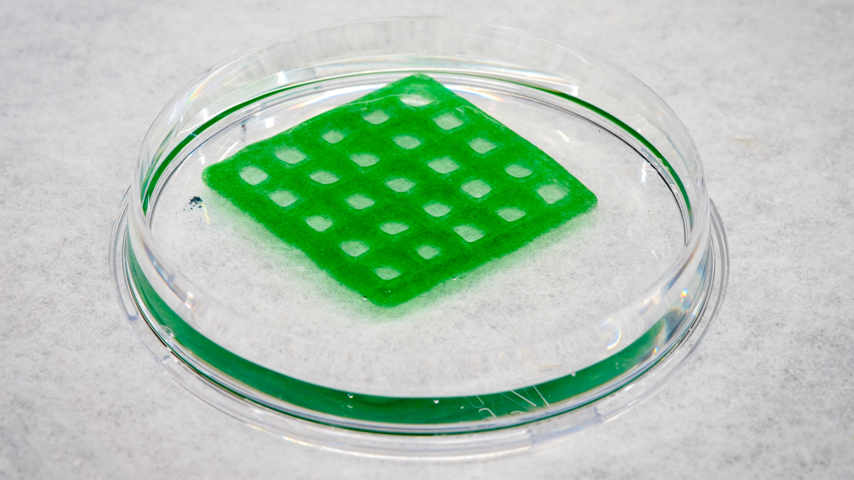
Genetically altered bacteria are fused with a polymer and 3D printed into a structure to remove pollutants from water.
By all accounts, the 1972 amendments to the Federal Water Pollution Control Act of 1948 have been successful in cleaning up the nation’s rivers and streams. But some pollutants remain and require more sophisticated methods of removal. Engineers and researchers are working on novel ways to handle the waste. Now, one team of researchers has taken the first step in developing a new type of material that may sustainably remove organic compounds.
A multidisciplinary team at the University of California, San Diego, has produced what they call an “engineered living material” that removes pollutants and then dissapates when the job is done. The material is a seaweed-based polymer that is combined with genetically engineered bacteria, and 3D printed into a filter. The bacteria produce an enzyme that transforms organic pollutants into harmless molecules.
“It’s combining a synthetic material like a polymer or a plastic with an engineered living system to provide a function that goes beyond what a traditional plastic would do,” said Jon Pokorski, a professor of nanoengineering who co-led the research. “Essentially we are using synthetic biology to program a microorganism to perform a function and embed that in the material.”
The work was performed by a collaboration of engineers, biologists, and materials scientists at the UC San Diego Materials Research Science and Engineering Center.
“We’re in nanoengineering, and there’s some really outstanding biologists specializing in cyanobacteria across the way,” said Pokorski. “I guess decontaminating water was an obvious choice [of a project] and kind of low-hanging fruit. All the components we use are pretty safe and pretty easy to work with. The enzymatic biology pathways are pretty straightforward and easy to implement, too.”
Team members created the new material with alginate, a polymer derived from seaweed. That was hydrated to make a gel and mixed with cyanobacteria, which then was loaded into a 3D printer. After some trial and error, they found that a grid-like structure worked best at keeping the bacteria alive. It also has a higher surface area to volume ratio, placing the bacteria near the surface and making decontamination more effective.
Become a Member: How to Join ASME
Researchers genetically engineered the bacteria to produce an enzyme called laccase, which has been shown to counteract a range of organic pollutants, including antibiotics, pharmacuetical drugs, dyes, and bisphenol A (BPA), a chemical used in the production of polycarbonate plastics. Specifically, the project used a pollutant called indigo carmine, a blue dye used to color denim.
Taking it a step further, they then developed a way to eliminate the bacteria after the pollutants were removed by engineering them to respond to the molecule theophylline. It triggers the bacterial to produce a protein that kills their cells.
“Think about algae that blooms on lakes,” said Pokorski. “We did not want that to happen. Basically, we wanted to make sure that we could turn them off, so just kill them when we’re done with the process. We don’t want any concern about having genetically modified bacteria in the environment.”
More for You: StampLike Device Treats Heart Disease, Then Dissolves
Pokorski said the work, published in the journal Nature Communications, started from scratch as there is little in the literature on the process. The overall goal is to make materials that respond to stimuli already present in the environment.
Looking back, he said one of the most difficult phases was at the beginning of the project, working with a team whose members had different diisciplines with different vocabularies. “When the biologists talked their jargon to me over the first several months, or even a year, it was just kind of Greek. I’m sure it was the same for them with me. Communication was a big challenge. And building cohesive and collaborative teams.”
Pokorski said the work is easily reproduced, and the next step is to show the entire range of pollutants to which it can be applied. With the great volume of microplastics now in the environment, he also wants to engineer bacteria that would actually degrade polymers.
“And right now our kill switch is programmed to respond to a specific molecule,” he said. “It would be better if it was programmed to respond to an environmental trigger, and I think we’re going to be working on that, too.”
John Kosowatz is senior editor.
A multidisciplinary team at the University of California, San Diego, has produced what they call an “engineered living material” that removes pollutants and then dissapates when the job is done. The material is a seaweed-based polymer that is combined with genetically engineered bacteria, and 3D printed into a filter. The bacteria produce an enzyme that transforms organic pollutants into harmless molecules.
“It’s combining a synthetic material like a polymer or a plastic with an engineered living system to provide a function that goes beyond what a traditional plastic would do,” said Jon Pokorski, a professor of nanoengineering who co-led the research. “Essentially we are using synthetic biology to program a microorganism to perform a function and embed that in the material.”
The work was performed by a collaboration of engineers, biologists, and materials scientists at the UC San Diego Materials Research Science and Engineering Center.
“We’re in nanoengineering, and there’s some really outstanding biologists specializing in cyanobacteria across the way,” said Pokorski. “I guess decontaminating water was an obvious choice [of a project] and kind of low-hanging fruit. All the components we use are pretty safe and pretty easy to work with. The enzymatic biology pathways are pretty straightforward and easy to implement, too.”
Team members created the new material with alginate, a polymer derived from seaweed. That was hydrated to make a gel and mixed with cyanobacteria, which then was loaded into a 3D printer. After some trial and error, they found that a grid-like structure worked best at keeping the bacteria alive. It also has a higher surface area to volume ratio, placing the bacteria near the surface and making decontamination more effective.
Become a Member: How to Join ASME
Researchers genetically engineered the bacteria to produce an enzyme called laccase, which has been shown to counteract a range of organic pollutants, including antibiotics, pharmacuetical drugs, dyes, and bisphenol A (BPA), a chemical used in the production of polycarbonate plastics. Specifically, the project used a pollutant called indigo carmine, a blue dye used to color denim.
Taking it a step further, they then developed a way to eliminate the bacteria after the pollutants were removed by engineering them to respond to the molecule theophylline. It triggers the bacterial to produce a protein that kills their cells.
“Think about algae that blooms on lakes,” said Pokorski. “We did not want that to happen. Basically, we wanted to make sure that we could turn them off, so just kill them when we’re done with the process. We don’t want any concern about having genetically modified bacteria in the environment.”
More for You: StampLike Device Treats Heart Disease, Then Dissolves
Pokorski said the work, published in the journal Nature Communications, started from scratch as there is little in the literature on the process. The overall goal is to make materials that respond to stimuli already present in the environment.
Looking back, he said one of the most difficult phases was at the beginning of the project, working with a team whose members had different diisciplines with different vocabularies. “When the biologists talked their jargon to me over the first several months, or even a year, it was just kind of Greek. I’m sure it was the same for them with me. Communication was a big challenge. And building cohesive and collaborative teams.”
Pokorski said the work is easily reproduced, and the next step is to show the entire range of pollutants to which it can be applied. With the great volume of microplastics now in the environment, he also wants to engineer bacteria that would actually degrade polymers.
“And right now our kill switch is programmed to respond to a specific molecule,” he said. “It would be better if it was programmed to respond to an environmental trigger, and I think we’re going to be working on that, too.”
John Kosowatz is senior editor.